Quick
brittle – a property applicable to a material if fracture occurs soon after the elastic limit is passed
ductile – a property applicable to a material if a large amount of plastic deformation takes place between the elastic limit and the fracture point
ductility – the ability of a material to be permanently deformed without breaking when the applied load is removed
Brittle and Ductile Materials
The stress-strain diagrams of various materials vary widely, and different tensile tests conducted on the same material may produce different results, depending upon the temperature of the specimen and the speed of loading. It is possible, however, to distinguish some common characteristics among the stress-strain diagrams of various groups of materials and to divide materials into two broad categories on the basis of these characteristics, namely, brittle materials and ductile materials. Typically brittle materials have a fracture strain less than 0.05 (∊f < 0.05) and ductile materials have a fracture strain greater than or equal to 0.05 (∊f ≥ 0.05).
 | test specimen |
 | brittle |
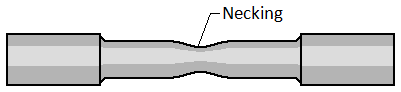
 | ductile |
Ductile materials deform much more than brittle materials.
Brittle materials fail suddenly, usually with no prior indication that collapse is imminent. On the other hand, ductile materials, such as structural steel, normally undergo a substantial deformation called yielding before failing, thus providing a warning that overloading exists.
Brittle Materials
Brittle materials, which comprise cast iron, glass, and stone, are characterized by the fact that rupture occurs without any noticeable prior change in the rate of elongation. Thus, for brittle materials, there is no difference between the ultimate strength and the breaking strength. Also, the strain at the time of rupture is much smaller for brittle than for ductile materials. From the figure, note the absence of any necking of the specimen in the case of a brittle material, and observe that rupture occurs along a surface perpendicular to the load. It is concluded from this observation that normal stresses are primarily responsible for the failure of brittle materials.
Ductile Materials
Ductile materials, which comprise structural steel, as well as may alloys of other metals, are characterized by their ability to yield at normal temperatures. As the specimen is subjected to an increasing load, its length first increases linearly with the load and at a very slow rate. Thus, the initial portion of the stress-strain diagram is a straight line with a steep slope. However, after a critical value σy of the stress has been reached, the specimen undergoes a large deformation with a relatively small increase in the applied load. This deformation is caused by slippage of the material along oblique surfaces and is due, therefore, primarily to shearing stresses. The elongation of the specimen after it has started to yield can be 200 times as large as its deformation before yield. After a certain maximum value of the load has been reached, the diameter portion of the specimen begins to decrease, because of local instability. This phenomenon is known as necking. After necking has begun, somewhat lower loads are sufficient to keep the specimen elongating further, until it finally ruptures. Rupture occurs along a cone-shaped surface which forms an angle of approximately 45° with the original surface of the specimen. This indicates that shear is primarily responsible for the failure of ductile materials, and confirms the fact that, under an axial load, shearing stresses are largest on surfaces forming an angle of 45° with the load.
Ductility measures the amount of deformation that a material can withstand without breaking. The distance between the gage marks on the test specimen can be measured before and after the test. The percent elongation describes the extent to which the specimen stretches before fracture:
where Lf is the distance between gage marks after the specimen breaks.
A second approach is to measure the percent change in cross-sectional area at the point of fracture before and after the test. The % reduction in area describes the amount of thinning undergone by the specimen during the test:
% reduction in area = | | × 100 |
where Af is the final cross-sectional area at the fracture surface.
Ductility is important to both designers and manufacturers. The designer of a component prefers a material that displays at least some ductility, so that, if the applied stress is too high, the component deforms before it breaks. Fabricators want a ductile material in order to form complicated shapes without breaking the material in the process.
Ductility, pronounced duhk TIHL uh tee, is the ability of certain solids to undergo permanent changes in shape without breaking. For example, a piece of copper can be drawn to make a thin wire. But the shape of a brick cannot be permanently changed except by breaking it.
Ductility is a valuable property of many metals, including aluminum, gold, iron, nickel, and silver. These metals can be drawn into wire, hammered into various shapes, or rolled into sheets. The term malleability is often used in place of ductility to describe the property of metals that allows them to be hammered into thin sheets. Metals are not the only ductile substances and not all metals are ductile. For example, modeling clay is a ductile nonmetallic substance and impure tungsten is a nonductile metal.